In the ever-evolving landscape of industrial innovation, few tools have had as profound an impact as the cordless drill. Once considered a niche convenience for DIY enthusiasts, today, it stands as a cornerstone of the industrial sector—essential for a broad range of applications from construction to manufacturing, and even aerospace engineering. As industries strive for greater efficiency, precision, and mobility, the cordless drill has proven itself as not just an accessory, but a critical tool driving productivity and innovation in countless sectors.
The Rise of the Cordless Drill in Industry
The cordless drill was introduced in the 1960s, revolutionizing how labor-intensive tasks were approached. Prior to its advent, industrial work was dominated by bulky, stationary power tools that tethered workers to power outlets. The introduction of battery-powered drills provided unmatched freedom, mobility, and versatility. Fast forward to today, and the cordless drill has become an indispensable part of the toolkit for industrial professionals around the globe.
According to Statista, the global market for power tools is expected to reach $52.12 billion by 2027, with the cordless tool segment experiencing some of the highest growth rates. This surge can be attributed to the increasing demand for high-efficiency, mobile, and versatile tools in sectors such as construction, automotive, and manufacturing.
Key Benefits of Cordless Drills for the Industrial Sector
- Mobility and Flexibility
One of the greatest innovations of the cordless drill is its mobility. With the elimination of cumbersome cords, workers can now access tighter spaces and move freely across job sites without being tethered to an outlet. This flexibility not only enhances productivity but also significantly improves safety by reducing trip hazards.
In industries like construction, the ability to maneuver easily between work areas or up scaffolding without worrying about an extension cord is invaluable. The ease of transport between different worksites or zones within a facility means a more efficient workflow and faster job completion.
- Efficiency and Speed
Cordless drills are engineered for speed and precision. With higher RPMs (rotations per minute) and better torque settings, modern cordless drills allow workers to complete tasks much faster than their manual counterparts. The integration of brushless motors in high-end models further enhances power output and energy efficiency.
For instance, DeWalt, a leader in power tools, reports that their cordless drills with brushless motors provide up to 57% more run-time and 30% more power compared to traditional brushed motors. In industries where speed directly correlates to output and cost-effectiveness, this increase in performance is a game-changer.
- Cost-Effectiveness
The initial investment in cordless drills might be higher than that of corded drills or manual tools. However, the long-term benefits far outweigh the cost. Cordless drills reduce operational downtime and minimize maintenance costs, as they are less likely to suffer from wear and tear due to the absence of cords or cables.
Additionally, the longer battery life of modern drills—often lasting an entire shift or more—translates to fewer interruptions, reduced battery replacements, and a streamlined workflow. For industries that operate on tight margins, the productivity boost provided by cordless drills is a crucial financial advantage.
Technological Advancements in Cordless Drills
The development of cordless drills has far outpaced expectations, with new features and innovations continuously pushing the limits of what these tools can achieve.
- Lithium-Ion Batteries
The development of lithium-ion batteries transformed the technology of cordless drills. In contrast to its predecessors, which were nickel-cadmium (NiCad) batteries, lithium-ion batteries are lighter, have a longer battery life, and recharge more quickly. Less waiting time in between jobs and fewer disruptions are the results of these enhancements.
A study by Research and Markets predicts that by 2025, lithium-ion battery-powered tools would account for 70% of the worldwide power tool industry, with cordless drills driving this trend. The benefits of lithium-ion technology are clear—improved performance, longer durability, and a significant reduction in battery maintenance costs.
- Smart Features and Connectivity
Newer models of cordless drills are embracing the Internet of Things (IoT). Manufacturers now offer drills equipped with smart features that enable real-time data monitoring, allowing users to track performance metrics such as battery life, torque, and operational status. This level of connectivity is invaluable for large-scale industrial operations, where fleet management of tools and maintenance scheduling can significantly impact productivity.
For example, Bosch has integrated smart features into their cordless drill models, offering tools that can sync with mobile apps to provide real-time diagnostic feedback, ensuring optimal performance throughout the workday.
Applications Across Industries
- Construction
In construction, cordless drills are used for tasks ranging from drilling holes in concrete to fastening bolts in heavy machinery. Their lightweight design makes them ideal for use in high places or challenging environments, such as confined spaces or overhead areas. Construction workers rely on the mobility and power of cordless drills to complete jobs efficiently and effectively.
- Automotive
In the automotive industry, cordless drills are employed to assemble parts, fasten screws, and install panels in vehicles. Their precision and power ensure that automotive assembly lines operate smoothly, with minimal downtime. For instance, in the assembly of electric vehicles, which require consistent and reliable power tools, the cordless drill is indispensable for assembling battery components and wiring systems.
- Manufacturing and Maintenance
In manufacturing plants, cordless drills serve as the go-to tool for maintenance and repair tasks. From repairing machinery to assembling product components, cordless drills enable workers to perform these tasks quickly and effectively. Their portability allows them to be used anywhere on the factory floor, reducing the need for centralized tool storage.
The Future of Cordless Drills in Industry
The future of cordless drills is bright, with innovations on the horizon that promise to make these tools even more versatile and efficient. The trend towards automation and smart technologies suggests that drills will continue to become smarter, integrating even more connectivity and data analytics into their design. Moreover, as industries become increasingly focused on sustainability, manufacturers are likely to enhance the energy efficiency of cordless drills, offering eco-friendly solutions that meet the growing demand for green tools.
Conclusion
The cordless drill has evolved from a simple power tool into an essential innovation that supports the industrial sector’s drive toward increased productivity, mobility, and precision. With advancements in battery technology, smart features, and industry-specific applications, cordless drills will continue to be at the forefront of industrial operations, reshaping workflows and driving efficiency in construction, automotive, and manufacturing sectors. As industries grow more reliant on these versatile tools, the cordless drill is poised to remain a critical enabler of modern industrial success.
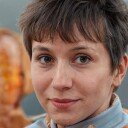
I have acted as a financial expert on the Today Show and Good Morning, America. I like to give reasonable advice on budgeting to people with any income level.